podpora on-line |
seriál Řezné nástroje, Technický tydeník, 2012Pro zjednodušení budeme pod pojmem soustružení rozumět vytváření cylindrických ploch na rotujícím obrobku, které jsou soustředné s jeho osou rotace (obr. 1).
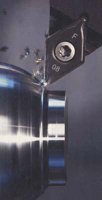 |
Obr. 1: Soustružení chápeme jako vytváření cylindrických ploch na rotujícím obrobku, které jsou soustředné s jeho osou rotace |
Nástroj, ve většině případů jednobřitý, je pevně upnut do suportu či revolverové hlavy obráběcího stroje. Tvar obrobku určuje i jeho upnutí - pokud je jeho štíhlost malá, stačí upnutí jen z jedné strany (do kleštiny nebo do sklíčidla); jako mezní se doporučuje poměr O D/L ? 2,5. U obrobků štíhlejších je nutné upnutí do hrotů či použití lunety a potom je také nutné zvažovat možné deformace obrobku způsobené vlastní hmotností a především řeznými a upínacími silami. Z mnoha hledisek se jedná o nejjednodušší způsob obrábění, je však velmi často používaným typem obráběcího procesu. Zhotovování vnějších i vnitřních závitů na rotujícím obrobku, jakož i jeho obrábění osovými nástroji (vrtáky apod.), které mají se soustružením mnoho společného, bude věnována zvláštní kapitola.
ZÁKLADNÍ TYPY SOUSTRUŽNICKÝCH OPERACÍ
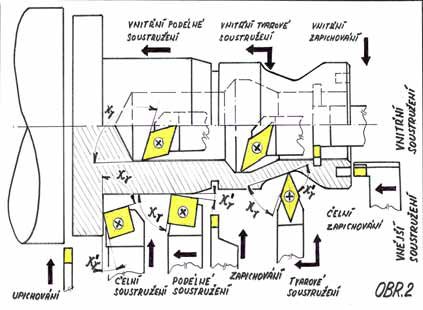 |
Obr. 2: Základní soustružnické operace
|
(obr. 2) Základní členění je na soustružení vnějších a vnitřních ploch. Jednotlivé operace se liší stabilitou řezných podmínek, náchylností ke vzniku vibrací, možnostmi přístupu nástroje k obráběné ploše, snadností odvodu vznikajících třísek, možností přívodu řezné kapaliny do blízkosti břitu nástroje a konečně vyložením užitého nástroje. Pokud se na obrobku opracovávají vnější i vnitřní plochy, doporučuje se z důvodu stability opracovat vnitřní plochy dříve než vnější.
Vnější soustružení podélné je nejběžnější soustružnická operace, při které se úhel nastavení hlavního břitu ?? při pohybu nástroje podél osy obrobku nemění buď vůbec, nebo jen v malém rozmezí, a proto lze snadno volit optimální řezné podmínky. Dostatek prostoru dovoluje dostatečně dimenzovat soustružnický nůž; je snížené nebezpečí vibrací a lze pracovat s maximální produktivitou . Vnější soustružení čela je rovněž častou operací; je charakterizováno velkými radiálními silami odtlačujícími obrobek, a proto se úhel nastavení volí mezi 45° – 75°, aby se zvětšila složka řezné síly ve směru osy rotace. Proti podélnému soustružení je soustružení čela komplikováno tím, že se během operace mění průměr, na kterém nástroj pracuje, a tedy i řezná rychlost. Může se proto vyskytnout oblast, kde dochází k tvorbě nárůstku a tím k místně zhoršené kvalitě opracovaného povrchu. Tento problém se dá částečně řešit změnou otáček vřetene soustruhu během operace.
Vnější upichování a zapichování se vyznačuje zvláštní geometrií nástroje, kde se oba vedlejší břity podílejí na zhotovení kvalitního povrchu. U upichování je problém se změnou řezné rychlosti ještě výraznější než u soustružení čela, protože břit nástroje dojíždí skoro k ose rotace. Odstranění zbylého výstupku na obrobeném povrchu se řeší nástrojem s nenulovým úhlem nastavení hlavního břitu. Zápichy jsou často velmi úzké a při upichování je snaha o maximální úsporu materiálu; proto nástroje pro tyto operace jsou velmi úzké a mají i zvláštní způsob upnutí břitové destičky.
Vnější soustružení tvarové charakterizují výrazné změny úhlu nastavení hlavního i vedlejšího ostří během operace. Úhel nastavení vedlejšího ostří ??´, tedy úhel, který svírá vedlejší ostří se směrem posuvu, určuje maximální možný úhel sklonu obráběného povrchu. Minimální úhel nastavení vedlejšího ostří během operace by měl být 2°, lépe však 7°, aby nedocházelo ke dření vedlejšího ostří o obrobený povrch. Z toho důvodu se kopírovací nástroje dodávají s úhlem špičky 55°, nověji 35° a dokonce 25°, aby se zvýšila možnost kopírování složitých profilů. Malý úhel špičky nástroje však snižuje její pevnost a omezuje řezné podmínky. Naproti tomu je výhodou možné opracování celého tvaru jedním nástrojem a úspora času pro jinak nutnou výměnu. Pokud se musí kopírovat osazení, je nutné volit úhel nastavení hlavního ostří větší než 90°; doporučuje se 93°. Čelní zapichování a úspěšná realizace axiálního zápichu podstatně závisí na správné volbě držáku, který musí odpovídat poloměru zakřivení drážky. Tvary držáků a břitových destiček pro různé průměry se výrazně liší; nesmí docházet k otírání nástroje o vnější ani o vnitřní stěnu drážky.
Vnitřní soustružení podélné a vnitřní soustružení tvaru charakterizuje velké vyložení nástroje, nutné pro práci v dutině, jeho snížená tuhost a sklon k vibracím. Jako největší doporučené vyložení nástroje se doporučuje poměr O D x L = 3 u standardních nástrojů. Nástroje se zvýšenou tuhostí, s jádrem ze slinutého karbidu nebo s tlumením vibrací dovolují zvýšit tento poměr až na hodnotu O D x L = 7. Řezné podmínky je nutno volit tak, aby se minimalizovala radiální složka řezné síly a pracuje se tedy s úhlem nastavení hlavního ostří blízkým 90°. Další nezbytností, které musí vyhovět řezné podmínky a zvolená geometrie nástroje, je vznik krátkých třísek, snadno odstranitelných z dutiny obrobku. Velkou roli při vnitřním soustružení hraje i správné nastavení břitu nástroje do osy rotace a správné použití řezné kapaliny, která musí nejen chladit a mazat břit nástroje, ale i vyplavovat vzniklé třísky. Vnitřní soustružení tvaru musí navíc vyhovět i komplikovaným kinematickým poměrům v omezeném prostoru obráběné dutiny.
Vnitřní zapichování vyžaduje tuhý nástroj, odolný proti vibracím, protože radiální složku řezné síly nelze z důvodu charakteru operace dostatečně snížit volbou úhlu nastavení. Zhotovování hlubokých zápichů je omezeno kinematickými poměry v dutině.
KVALITA OBROBENÉHO POVRCHU
je ovlivněna jednak řeznými podmínkami, jednak vlastnostmi obráběného materiálu a tuhostí soustavy stroj – nástroj – obrobek. Se zvětšujícím se poloměrem špičky se zlepšuje kvalita opracovaného povrchu, zhoršuje se ale tvorba třísky a směr a velikost radiální složky řezné síly. Zvyšující se posuv na otáčku sice zvyšuje úběr za jednotku času, ale zhoršuje kvalitu povrchu. Řešení nabízí hladicí destičky („Wiper“), které díky malému úhlu nastavení vedlejšího ostří seřezávají nerovnosti a vytváří hladší povrch. Obecně platí, že při užití hladicí destičky se dvakrát zlepší drsnost povrchu oproti povrchu obrobenému týmž posuvem klasickou destičkou, anebo použitím hladicí destičky lze dvakrát zvýšit posuv oproti práci s klasickou destičkou při stejné drsnosti (obr. 3). Pro snazší porovnání jsou ve všech zobrazených variantách úhel špičky, úhel nastavení hlavního ostří a hloubka řezu stejné. Negativním jevem je tvorba otřepu, především při obrábění měkkých materiálů. Pomoci může zmenšení úhlu nastavení hlavního ostří a použití nástroje s ostřejším břitem a pozitivní geometrií. Vznik vibrací, nedostatečná tuhost obrobku a jeho upnutí vytvářejí charakteristický, tzv. pochvělý povrch. Řešením je zvýšit stabilitu upnutí obrobku, snížit hloubku řezu a tloušťku třísky, zmenšit vyložení nástroje.
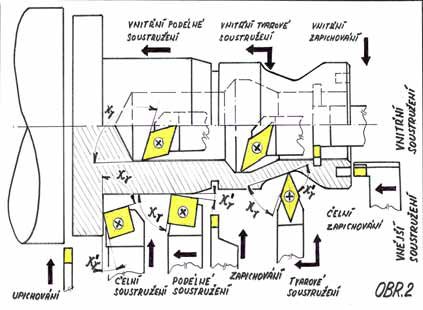 |
Obr. 3: Vliv provedení špičky na drsnost povrchu
|
VOLBA NÁSTROJE, VOLBA ŘEZNÝCH PODMÍNEK
Pokud se nevychází z čisté empirie a je snaha se dobrat optimálního řešení, jde o záležitost komplexního charakteru, která musí nezbytně postihovat řadu aspektů. Prvním z nich je počáteční analýza, zahrnující rozbor součásti – její velikost, stabilitu, způsob upnutí, velikost výrobní série, požadavky na kvalitu a typ operace. Následuje zhodnocení stroje, který je k dispozici, z hlediska výkonu, stability, konfigurace a způsobu možného užití řezné kapaliny. Dále je zapotřebí přiřadit obráběný materiál do jedné ze šesti skupin dle ISO 513 a vyhodnotit danou operaci dle jejího charakteru (dokončovací soustružení, polohrubovací či hrubování).
Na základě těchto údajů lze zvolit průřez držáku (pokud již není dán jednoznačně strojem), typ upnutí vyměnitelné břitové destičky, povolenou kombinaci hloubky řezu a posuvu na otáčku. Pro předem zvolenou břitovou destičku a daný materiál se určí typ utvářeče a konečně, na základě těchto vstupních hodnot se volí startovní řezná rychlost dle doporučení výrobce. Tuto startovní řeznou rychlost pak lze korigovat na základě skutečného technického stavu obráběcího stroje, skutečné tvrdosti obráběného materiálu, použití řezných kapalin, a zvláštních požadavků na jakost obrobeného povrchu a životnosti nástroje.
Ing. Petr Borovan, převzato z Technického týdeníku
podrubriky seriál Řezné nástroje, Technický tydeník, 2012: