podpora on-line |
seriál Řezné nástroje, Technický tydeník, 2012PŘEMĚNA ZBYTKOVÉHO AUSTENITU POMOCÍ KAPALNÉHO DUSÍKU
Životnost nástrojů závisí především na tvrdosti a odolnosti proti opotřebení. Všechny technologie směřující ke zvyšování životnosti jsou velmi důležité. Neopomenutelným předpokladem pro bezvadnou funkčnost mnohých nástrojů je jejich rozměrová stálost a odstranění vnitřního pnutí. Dodatečné změny těchto vlastností, a to například přeměnou zbytkového austenitu během jejich používání, jsou příčinou zmetkovitosti a následných reklamací. Tím je ovlivněna výše nákladů vynaložených na dodatečnou úpravu, resp. výměnu nástroje a s tím i související doba na opravu a doba prostoje.
Řízená přeměna zbytkového austenitu kombinací obvyklých technologií tepelného zpracování se zmrazováním je často technicky i ekonomicky nejvhodnější metoda, jak dosáhnout požadovaných vlastností materiálu. Teplota kapalného dusíku (–196 °C) se dříve využívala pouze pro tzv. přímé chlazení ponorem, v dnešní době se využívá převážně pro chlazení v mrazicích skříních a boxech. Společnost Messer dodává nejen kapalný dusík, ale současně také technologie a zařízení ke kontrolovanému i reprodukovatelnému provádění procesů zmrazování, které jsou zapotřebí ke spolehlivé přeměně zbytkového austenitu na martenzit.
TEORETICKÉ PODKLADY
Kalení oceli spočívá v tom, že se po austenitizaci z teploty nad Ac3 materiál prudce zchladí a austenit se přemění na martenzit. Tvrdost a odolnost vůči opotřebení závisí jednak na složení oceli a jednak na její prokalitelnosti. Zejména obsah uhlíku určuje jak počáteční teplotu vzniku martenzitu Ms, při níž se během prudkého zchlazování začíná vytvářet martenzit, tak i teplotu ukončení tvorby martenzitu Mf, pod níž je proces martenzitické přeměny prakticky ukončen.
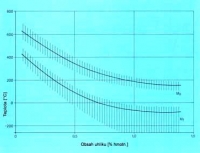
Na obr. 1 je znázorněn průběh těchto teplot podle obsahu uhlíku u nelegované oceli. Pásmo rozptylu je znázorněno jako vyšrafovaná plocha. Podle obr. 1 dosahuje Mf při obsahu uhlíku C = 0,5 % hm. teploty okolí. U ocelí s obsahem C > 0,5 % hm. dochází v důsledku ještě neukončeného vytváření martenzitu (při zchlazení na teplotu okolí) ke vzniku zbytkového austenitu (20–30 % hmot. u nástrojových ocelí).
Z obr. 1 rovněž vyplývá, že teplota ukončení tvorby martenzitu může podle přesnosti dnešních zjišťovacích metod dosahovat až pásma teploty asi –200 °C i níže. Vytvářené podíly martenzitu se s klesající teplotou zvyšují a lze je popsat pro oceli vhodné k zušlechťování na základě rovnice:

Na obr. 2 je znázorněno, jak dochází k tvorbě martenzitu M při malém a velkém obsahu uhlíku v závislosti na teplotě chlazení. V případě malého obsahu uhlíku dochází k úplné přeměně, u velkého obsahu uhlíku přetrvávají podíly zbytkového austenitu (Az). Ty jsou však při zchlazení na úroveň teploty zkapalněného dusíku podstatně nižší než při teplotě prostředí. Jak je patrné z tohoto stručného shrnutí, rozhodující faktory k vytváření zbytkového austenitu jsou již velmi dobře známy. Proto záleží na jednotlivých kalírnách, aby s použitím vhodných procesů tepelného zpracování upravily obsah zbytkového austenitu na požadovanou hodnotu.
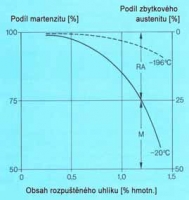
ZPRACOVÁNÍ ZMRAZOVÁNÍM - JAK A PROČ?
Přeměny austenitu lze dosáhnout (podle chemického složení oceli) již základním procesem zušlechťování, resp. opakovaným popouštěním, což potvrzují i praktické zkušenosti. Několikrát opakovaný cyklus zahřátí, výdrže a zchlazení je proto v mnoha případech nezbytný, ale současně časová náročnost takového procesu a spotřeba elektrické energie je velmi vysoká. Proto se hledají jiná, alternativní řešení. Stále častěji používanou technologií, hlavně u ocelí s vysokým podílem zbytkového austenitu, je technologie zmrazování, která musí přímo navazovat na obvyklé kalení tak, aby se zamezilo stabilizaci stále přítomného zbytkového austenitu. Zejména na začátku zakalení musí být rychlost zchlazování dostatečně vysoká, aby zůstala zachována celková austenitová struktura, dokud nebude dosažena počáteční teplota pro vznik martenzitu Ms. Pak musí být rychlost zakalení tak nízká, aby při vytváření martenzitu nevznikala příliš velká lomová napětí a nemohlo docházet k deformacím materiálu.
POUŽITÍ KAPALNÉHO DUSÍKU
Kapalný dusík lze využít několika způsoby. Mezi základní varianty patří např. přímé zmrazování ponorem, mražení pomocí sekundární organické látky (metylcyklohexan nebo trichloretylen) a v současné době nejpoužívanější zchlazování nástřikem kapalného dusíku do chladicího prostoru mrazicí skříně.
PŘÍMÉ ZMRAZOVÁNÍ PONOREM
Metoda „přímého zmrazování ponorem“ nachází uplatnění např. při běžném dílenském nalisování hřídele, která má pokojovou teplotu, do náboje lokálně předehřátého. Ohřevem ovšem docházelo k lokálnímu tepelnému ovlivnění náboje a následně ke vzniku mikrotrhlin. Jako alternativu lze uplatnit obdobný postup, pouze se použije hřídel zchlazená kapalným dusíkem a náboj při teplotě okolí. Vyloučí se vliv předehřevu a spoj vykazuje lepší mechanické vlastnosti.
ZCHLAZOVÁNÍ NÁSTŘIKEM KAPALNÉHO DUSÍKU DO CHLADICÍHO PROSTORU MRAZICÍ SKŘÍNĚ
Základem technologie je vstřikování kapalného dusíku tryskami do chladicího prostoru skříně. Ventilátory rozhánějí dusík do všech míst tak, aby rovnoměrně působil na zpracovávaný materiál. V současné době jsou k dispozici dvě základní konstrukční řešení mrazicích skříní. Bez ohřevu a s ohřevem pomocí topných těles. Pracovní postupy obou skříní jsou ovšem odlišné. Běžný pracovní postup mrazicí skříně bez ohřevu je takový, že procesní regulátor pomocí termočlánků řídí pouze proces zchlazení a výdrže. Po ukončení výdrže se otevřou dveře, materiál se vyjme a nechá se přirozeně ohřát v hale na teplotu okolí. Tento postup ovšem způsobí „ojínění“ materiálu vzdušnou vlhkostí a takový materiál je náchylnější na korozi. Lze ponechat materiál i ve skříni bez ohřevu, dokud se přirozeně neohřeje na teplotu okolí, to ovšem může trvat i několik dní. U skříní s ohřevem termočlánky monitorují nejen proces mražení, ale i ohřevu. Na regulačním panelu se programuje celý pracovní režim, tedy rychlost a čas zchlazování, doba výdrže a rychlost i čas ohřevu. Pracovní teploty takové mrazicí skříně se pohybují od asi –180 do +200 °C. Výhodou mrazicích skříní s řízeným ohřevem je, že celý proces ohřevu až na teplotu okolí probíhá přímo ve skříni bez přístupu vzduchu a nedochází tak k nežádoucímu jevu „ojínění“. Další výhodou je podstatné zkrácení času z teploty výdrže na teplotu okolí. Spotřebu dusíku ovlivňuje celá řada faktorů, např. hmotnost vsázky, rozložení a členitost zpracovávaných dílů, druh izolace skříně, teplota zmrazení atd., ale na základě praktických zkušeností lze konstatovat, že specifické spotřeby jsou asi 2 kg kapalného dusíku na 1 kg materiálu.
PŘÍKLADY POUŽITÍ ZMRAZOVÁNÍ
Případ 1: Rychlořezná ocel Obvyklý postup při zpracování nožů na řezání závitů (0,85 % C, 6 % W, 5 % Mo, 4 % Cr, 1 % V) spočíval v kalení do oleje, přičemž vznikala tvrdost 63 HRC. Následně se provedlo 3krát popouštění, dvakrát při teplotě 560 °C a jednou při teplotě 590 °C, vždy po dobu 2 h, čímž se dosáhlo konečné tvrdosti 62 HRC. Úprava zmrazováním spočívala v tom, že se materiál zakalil stejným způsobem, pak proběhlo okamžité zmrazení na teplotu –100 °C, čímž se tvrdost zvýšila na 68 HRC. Následně proběhlo pouze jedno popouštění při teplotě 600 °C po dobu 2 h, čímž vznikla konečná tvrdost 64 HRC. Tímto zpracováním se snížila doba cyklu a dosáhlo se lepších mechanických vlastností.
Případ 2: Různé nástrojové oceli Měřila se tvrdost a odolnost vůči opotřebení u různých nástrojových ocelí, které po obvyklém tepelném zpracování ještě vykazovaly zbytkový austenit. Následně se vzorky zpracovaly zmrazováním, a to jednou při teplotě –80 °C a podruhé při teplotě –150 °C, a opět se změřily. Zatímco rozdíly v tvrdosti byly pouze zanedbatelné, došlo především k výraznému zvýšení odolnosti vůči opotřebení.
SHRNUTÍ
Podle uvedených souvislostí týkajících se přeměny zbytkového austenitu je možné shrnout výhody, kterých lze dosahovat použitím technologie zmrazování:
Vyšší tvrdost a větší odolnost vůči opotřebení
Rozměrová stálost a odstranění vnitřního pnutí
Zkrácení procesu zušlechťování o asi 15–20 %
Ing. Jiří Svatoš, aplikační inženýr – tepelné zpracování kovů Messer Technogas s. r. o., převzato z Technického týdeníku