podpora on-line |
seriál Řezné nástroje, Technický tydeník, 2012Řezné materiály povlakované tvoří v současné době většinu nabídky na trhu; řezné povlaky dovolují podstatným způsobem zvýšit řezné rychlosti, posuvy i životnosti povlakovaného řezného karbidu proti nepovlakovanému, pokroky v povlakovacích technologiích dovolují dodat optimální povlak pro konkrétní způsob použití a tím výrazně zvýšit užitnou hodnotu řezného nástroje.
Požadavky kladené na povlaky řezných nástrojů
Tab 1: Vybrané druhy povlaků dle chemického složení a jejich určení
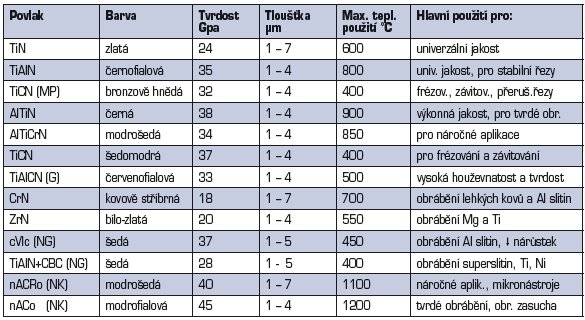
Vysvětlivky: MP – víceúčelový povlak, CBC – dia povlak, G – gradientní struktura povlaku,
NG – nanogradientní struktura, NK – nanokompozitní struktura
Pro srovnání: tvrdost oceli kalené na 63 HRc činí cca 8 Gpa, tvrdost nepovlakovaného WC – 18 Gpa, tvrdost
polykrystalického diamantu (PCD) – 80 až 90 Gpa
Tab 2: První volba povlaku podle způsobu použití
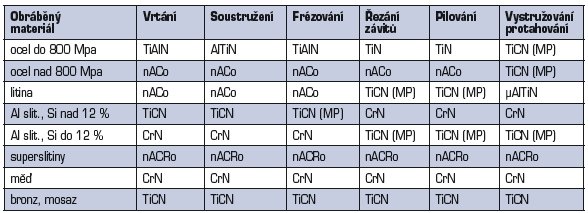
Tab 3:
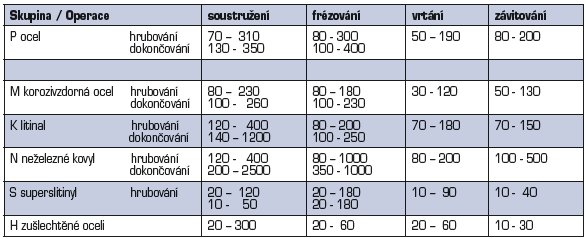
Tab 4:
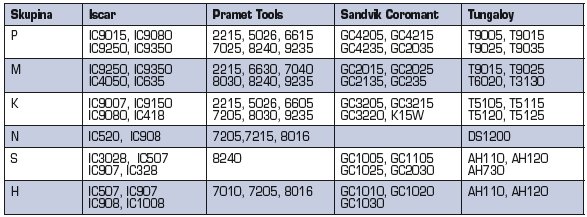
Prvotním požadavkem je vysoká tvrdost, která zvyšuje odolnost proti opotřebení; žádoucí odolnost proti mechanickým rázům, vznikajícím při přerušovaném řezu či frézování, dodává povlakovanému nástroji potřebná houževnatost. Povlak musí být odolný proti vzniku trhlin, musí vytvářet tepelnou a chemickou bariéru mezi třískou a substrátem, aby nedošlo k degradaci substrátu za vysokých teplot, vznikajících při obrábění náročných materiálů nebo vysokými řeznými podmínkami. Povlak s nízkým součinitelem tření usnadňuje odchod třísek a zvyšuje odolnost proti tvoření nárůstku a odolnost proti opotřebení hřbetu. Dostatečná přilnavost povlaku vůči substrátu je podmínkou spolehlivosti řezného procesu; v neposlední řadě se vyžaduje i spolehlivá predikce životnosti, která je podmínkou optimálního plánování řezné operace. Mají-li být všechny tyto požadavky splněny pro nejrůznější typy obráběcích operací, řezných nástrojů a obráběných materiálů, je zřejmé, že i přes snahu po univerzalitě povlaků vzniká a je komerčně nabízeno široké spektrum řezných povlaků.
Technologie nanášení
Povlaky nanášené PVD metodou (Physical Vapour Deposition – fyzikální nanášení povlaku) jsou nanášeny za teplot 400 °C – 600 °C (obr. 1); díky své tvrdosti propůjčují povlakovanému materiálu odolnost proti otěru a vnitřní tlaková pnutí zvyšují houževnatost. Malá tloušťka povlaku dovoluje zhotovit ostrý břit. Vhodné jsou proto aplikace na monolitních karbidových frézách, středových břitových destičkách vrtáků, pro zapichování a řezání závitů; jsou široce využívány pro dokončovací aplikace. Možno st vytváření velmi tenkých vrstev se využívá při zhotovování vícevrstvých či mnohovrstvých povlaků, kde kombinace vrstev s různými vlastnosti umožňuje zhotovit optimální povlak pro zamýšlený způsob použití (obr. 2, 3). Tloušťka povlaku se obecně pohybuje od 1,8 µm do 3 µm; u vícevrstvých povlaků může tloušťka jedné vrstvy činit zhruba 0,2 až 0,8 µm a u nanopovlaků, skládajících se z mnoha vrstev, tloušťka vrstvy obnáší méně než 0,2 µm. U gradientních povlaků se složení plynule mění od substrátu směrem k povrchu, který lze obdržet jako velmi tvrdý.
Povlaky nanášené CVD metodou (Chemical Vapour Deposition - chemické nanášení povlaku) mají vyšší tvrdost a větší tloušťky – 2 až 16 µm – ve srovnání s PVD povlaky. Vyznačují se vysokou odolností proti otěru a výbornou adhezí k podkladu, a proto jsou první volbou v širokém spektru aplikací – ve všeobecném soustružení, vyvrtávání oceli, na obvodových břitových destičkách vrtáků a frézování v materiálech ISO P, M a K. Jejich nevýhodou je vysoká teplota nanášení, která se pohybuje mezi 700 °C – 1050 °C a může negativně ovlivnit vlastnosti podkladového materiálu. Proto se v poslední době zavádí technologické modifikace s nižšími teplotami – technologie MT-CVD a PACVD.
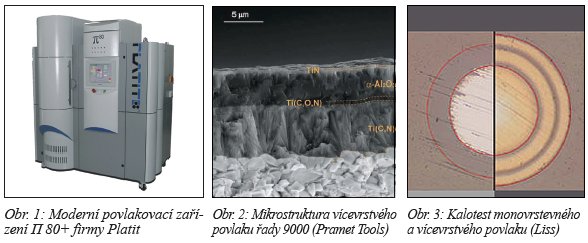
Ilustrativní řezné rychlosti
Zde uvedené rychlosti (vc uvedené v m/min) slouží pouze pro ilustraci možností moderních řezných materiálů; konkrétní volba musí brát ohled na konkrétní řezný materiál, řezné podmínky (posuv, hloubku řezu a geometrii nástroje), detailní specifikaci obráběného materiálu (obrobitelnost, typ obráběcí operace - např. přerušovaný řez, hrubování či dokončování, priorita životnost versus produktivita), na charakteristiku obrobku a stroje atd. a je účelné řezné podmínky konzultovat s dodavatelem vybraného řezného nářadí.
Výběr moderních řezných materiálů z nabídky předních výrobců
V nabídce renomovaných výrobců jsou desítky řezných materiálů, nabízených pod nejrůznějšími obchodními názvy. Jejich vzájemné porovnání je obtížné, protože jednotlivé typy se z hlediska určení navzájem plně nekryjí. Pro zjednodušení obsahuje uvedené porovnání pouze několik výrobců a jen CVD a PVD řezné materiály.
Ing. Petr Borovan, převzato z Technického týdeníku